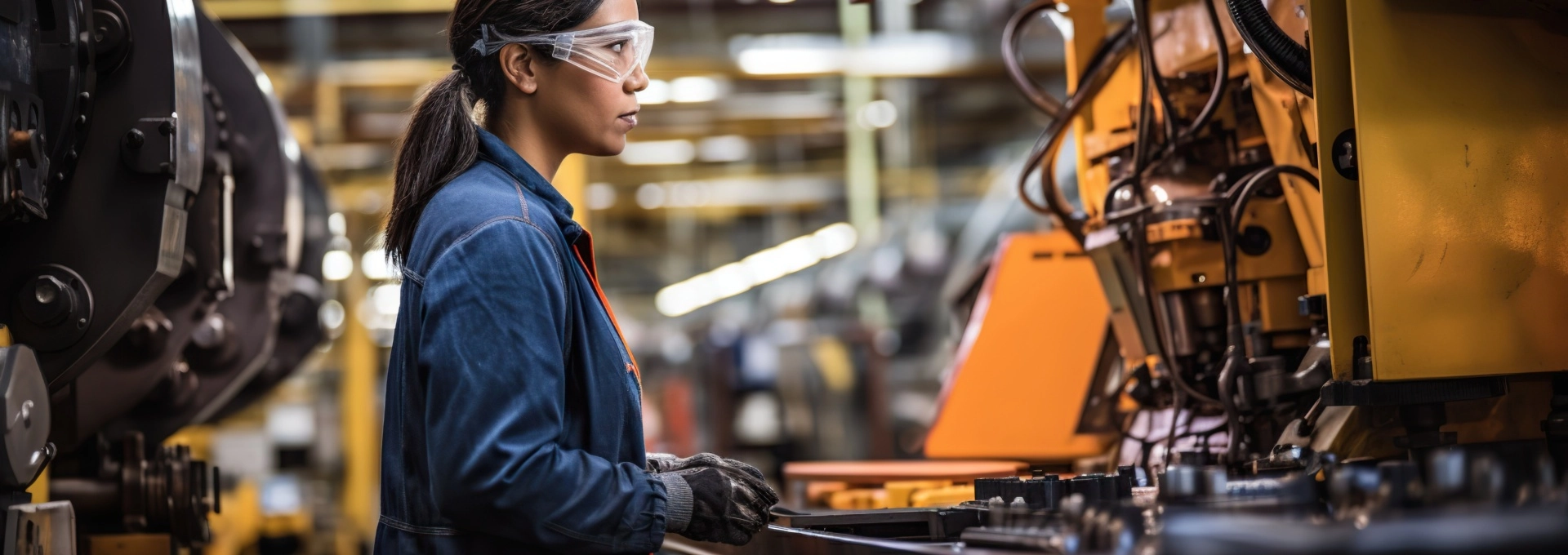
L'optimisation de la chaîne de production est un enjeu majeur pour toute entreprise industrielle soucieuse d'améliorer sa compétitivité. Dans un contexte économique de plus en plus concurrentiel, la capacité à produire efficacement tout en maintenant une qualité élevée est devenue cruciale. Les entreprises qui parviennent à optimiser leurs processus de fabrication bénéficient d'avantages considérables : réduction des coûts, augmentation de la productivité, amélioration de la qualité des produits et satisfaction accrue des clients.
Analyse des étapes clés du processus industriel
La première étape incontournable pour optimiser votre chaîne de production est de réaliser une analyse approfondie de l'ensemble du processus industriel. Cette phase d'audit permet d'identifier les forces et faiblesses de votre système actuel et de repérer les opportunités d'amélioration. Pour mener à bien cette analyse, il est recommandé de suivre une approche méthodique en examinant chaque étape du processus de fabrication. L'optimisation de la chaîne de production passe par une analyse rigoureuse.
Identifier les goulots d'étranglement de la production
Les goulots d'étranglement sont les points de votre chaîne de production qui limitent le débit global et réduisent l'efficacité du système. Il est crucial de les identifier précisément pour pouvoir ensuite les éliminer. Pour ce faire, vous pouvez utiliser des outils d'analyse comme le diagramme de Gantt ou la cartographie de flux de valeur (VSM
). Ces méthodes permettent de visualiser l'ensemble du processus et de repérer les étapes qui ralentissent la production.
Une fois les goulots d'étranglement identifiés, il convient d'analyser leurs causes profondes. S'agit-il d'un problème d'équipement, de manque de personnel qualifié, ou d'une mauvaise organisation du travail ? La réponse à ces questions guidera vos actions d'optimisation.
Évaluer l'efficacité des équipements et machines
L'évaluation de l'efficacité des équipements est un autre aspect important de l'analyse du processus industriel. Le Taux de Rendement Synthétique (TRS) est un indicateur clé pour mesurer la performance globale des machines. Il prend en compte trois facteurs : la disponibilité, la performance et la qualité. Un TRS élevé indique une utilisation optimale des équipements, tandis qu'un TRS faible révèle des opportunités d'amélioration.
Pour calculer le TRS, utilisez la formule suivante :
TRS = Disponibilité x Performance x Qualité
Où :
- Disponibilité = Temps de fonctionnement réel / Temps de fonctionnement planifié
- Performance = Cadence réelle / Cadence théorique
- Qualité = Nombre de pièces bonnes / Nombre total de pièces produites
En analysant ces différents facteurs, vous pourrez identifier les axes d'amélioration pour chaque équipement de votre chaîne de production.
Examiner les flux de matériaux et produits
L'optimisation des flux de matériaux et de produits est essentielle pour améliorer l'efficacité globale de votre chaîne de production. Une analyse détaillée des mouvements de matières premières, de produits semi-finis et de produits finis vous permettra d'identifier les déplacements inutiles, les zones de stockage inadaptées ou les temps d'attente excessifs.
Pour visualiser ces flux, vous pouvez utiliser un diagramme de spaghetti. Cet outil simple mais efficace consiste à tracer sur un plan de l'usine tous les déplacements effectués par les matériaux et les opérateurs. Il met en évidence les inefficacités dans l'agencement de votre atelier et vous aide à optimiser les parcours.
L'analyse approfondie du processus industriel est la pierre angulaire de toute démarche d'optimisation. Elle vous fournit une vision claire des points à améliorer et vous guide dans la définition des actions prioritaires à mettre en œuvre.
Optimisation de l'agencement des postes de travail
Une fois l'analyse du processus industriel réalisée, l'optimisation de l'agencement des postes de travail constitue une étape cruciale pour améliorer l'efficacité de votre chaîne de production. Un agencement bien pensé permet de réduire les déplacements inutiles, d'améliorer la circulation des flux et de créer un environnement de travail plus ergonomique pour vos opérateurs.
Pour optimiser l'agencement de vos postes de travail, suivez ces étapes :
- Cartographiez le flux de production actuel
- Identifiez les zones de congestion et les déplacements superflus
- Réorganisez les postes de travail en fonction du flux optimal
- Veillez à l'ergonomie des postes pour améliorer le confort et la sécurité des opérateurs
- Testez le nouvel agencement et ajustez si nécessaire
L'application des principes du lean manufacturing peut grandement vous aider dans cette démarche. Par exemple, la méthode des 5S (Seiri, Seiton, Seiso, Seiketsu, Shitsuke) permet d'organiser l'espace de travail de manière efficace et standardisée. Elle se concentre sur l'élimination du superflu, le rangement, le nettoyage, la standardisation et la discipline.
N'oubliez pas que l'optimisation de l'agencement des postes de travail est un processus continu. Il est important de réévaluer régulièrement votre organisation pour l'adapter aux évolutions de votre production et aux retours de vos opérateurs.
Mise en place d'indicateurs de performance pertinents
Pour piloter efficacement votre chaîne de production et mesurer les progrès réalisés, il est essentiel de mettre en place des indicateurs de performance pertinents. Ces Key Performance Indicators (KPI) vous permettront de suivre en temps réel l'efficacité de vos processus et de prendre des décisions éclairées pour les optimiser. Une bonne stratégie d'optimisation de la chaîne de production repose sur un suivi précis des indicateurs clés.
Définir des KPI adaptés à votre industrie
Le choix des KPI doit être guidé par les spécificités de votre industrie et les objectifs stratégiques de votre entreprise. Voici quelques exemples d'indicateurs couramment utilisés dans l'industrie manufacturière :
- Taux de Rendement Synthétique (TRS)
- Taux de rebut
- Temps de cycle
- Coût unitaire de production
- Taux de respect des délais de livraison
Il est important de ne pas multiplier les indicateurs à l'excès. Concentrez-vous sur 5 à 7 KPI vraiment stratégiques pour votre activité. Assurez-vous également que ces indicateurs soient SMART : Spécifiques, Mesurables, Atteignables, Réalistes et Temporellement définis.
Suivre l'évolution des indicateurs en temps réel
Pour tirer pleinement parti de vos KPI, il est crucial de pouvoir les suivre en temps réel. L'utilisation d'un système de gestion de la production assistée par ordinateur (GPAO
) vous permettra de collecter et d'analyser les données de production en continu. Ces outils offrent généralement des tableaux de bord personnalisables qui vous donnent une vision claire et instantanée de la performance de votre chaîne de production.
La mise en place d'afficheurs visuels dans l'atelier peut également être bénéfique. Ces écrans, visibles par tous les opérateurs, affichent les principaux KPI et leur évolution, favorisant ainsi l'implication de chacun dans la démarche d'amélioration continue.
Utiliser les données pour prendre des décisions
La collecte de données n'a de sens que si elle aboutit à des actions concrètes. Analysez régulièrement l'évolution de vos KPI pour identifier les tendances et les écarts par rapport à vos objectifs. Organisez des réunions d'équipe pour discuter des résultats et définir des plans d'action d'amélioration.
N'hésitez pas à utiliser des outils d'analyse statistique comme les cartes de contrôle ou les diagrammes de Pareto pour approfondir votre compréhension des données. Ces méthodes vous aideront à distinguer les variations normales des problèmes systémiques nécessitant une intervention.
Les indicateurs de performance sont le tableau de bord de votre chaîne de production. Ils vous guident dans vos décisions et vous permettent de mesurer concrètement les progrès réalisés.
Formation et implication du personnel de production
L'optimisation de votre chaîne de production ne peut se faire sans l'implication active de votre personnel. Les opérateurs sont en première ligne et possèdent une connaissance précieuse des processus de fabrication. Leur formation et leur engagement sont donc essentiels pour réussir votre démarche d'amélioration continue.
Sensibiliser les équipes aux enjeux de l'optimisation
La première étape consiste à expliquer clairement à l'ensemble du personnel les objectifs de la démarche d'optimisation et les bénéfices attendus, tant pour l'entreprise que pour les employés eux-mêmes. Organisez des sessions d'information pour présenter les concepts clés du lean manufacturing et les indicateurs de performance que vous avez choisis.
Utilisez des exemples concrets tirés de votre propre production pour illustrer les enjeux. Par exemple, montrez comment une réduction du taux de rebut peut se traduire par une augmentation de la productivité et potentiellement par des primes pour les équipes.
Développer les compétences techniques des opérateurs
Pour optimiser votre chaîne de production, il est crucial que vos opérateurs maîtrisent parfaitement leurs équipements et les procédures de travail. Mettez en place un plan de formation continue qui couvre à la fois les aspects techniques et les méthodes d'amélioration continue.
Voici quelques domaines de formation à considérer :
- Utilisation optimale des machines et équipements
- Techniques de résolution de problèmes (ex : méthode PDCA, 8D)
- Outils du lean manufacturing (5S, SMED, TPM)
- Qualité et contrôle statistique des processus
N'oubliez pas de former également vos opérateurs à l'utilisation des outils de suivi des KPI que vous avez mis en place. Plus ils seront à l'aise avec ces outils, plus ils seront en mesure de contribuer activement à l'optimisation de la production.
Encourager les suggestions d'amélioration des collaborateurs
Pour tirer pleinement parti de l'expertise de vos opérateurs, mettez en place un système de suggestions d'amélioration. Encouragez activement vos collaborateurs à partager leurs idées pour optimiser les processus, réduire les gaspillages ou améliorer la qualité. Voici quelques pistes pour favoriser cette démarche participative :
- Installez des boîtes à idées dans l'atelier
- Organisez régulièrement des réunions d'équipe pour discuter des propositions
- Mettez en place un système de récompense pour les meilleures suggestions
- Communiquez sur les améliorations mises en œuvre grâce aux idées des opérateurs
N'oubliez pas que les opérateurs sont les mieux placés pour identifier les inefficacités au quotidien. Leur implication est donc importante pour une optimisation durable de votre chaîne de production. Une implication active du personnel est essentielle pour une optimisation réussie de la chaîne de production.
La formation et l'implication du personnel sont les piliers d'une démarche d'amélioration continue réussie. Investissez dans vos équipes pour transformer votre culture d'entreprise et stimuler l'innovation à tous les niveaux.
Intégration des technologies de l'industrie 4.0
L'optimisation de votre chaîne de production passe également par l'intégration des technologies de l'industrie 4.0. Ces innovations permettent d'améliorer la connectivité, l'automatisation et l'analyse des données tout au long du processus de fabrication. Considérez par exemple l'automatisation du processus picking, qui permet d'accélérer et de fiabiliser la préparation des commandes. Voici quelques technologies clés à considérer pour moderniser votre processus industriel :
L'Internet des Objets Industriel (IIoT)
L'IIoT consiste à équiper vos machines et équipements de capteurs connectés. Ces capteurs collectent en temps réel une multitude de données sur le fonctionnement de votre chaîne de production : températures, vibrations, consommation d'énergie, etc. L'analyse de ces données permet de :
- Détecter précocement les anomalies et prévenir les pannes
- Optimiser les paramètres de production en temps réel
- Mettre en place une maintenance prédictive
L'intelligence artificielle et le machine learning
L'IA et le machine learning permettent d'exploiter pleinement le potentiel des données collectées par l'IIoT. Ces technologies peuvent analyser des volumes massifs de données pour :
- Prédire les pannes et optimiser la maintenance
- Ajuster automatiquement les paramètres de production
- Optimiser la planification de la production
- Détecter les défauts de qualité
La réalité augmentée
La réalité augmentée (RA) trouve de nombreuses applications dans l'industrie manufacturière. Cette technologie peut être utilisée pour :
- Former les opérateurs à de nouvelles tâches ou procédures
- Guider les techniciens lors des opérations de maintenance
- Visualiser des informations en temps réel sur les équipements
L'impression 3D
L'impression 3D, ou fabrication additive, peut révolutionner certains aspects de votre chaîne de production. Cette technologie permet de :
- Produire rapidement des prototypes ou des petites séries
- Fabriquer des pièces de rechange à la demande
- Créer des outils ou des gabarits personnalisés